Description
Differential pressure instruments according to ISO 5167 are used in most industrial sectors. The available range of different throttling devices and materials allows measurement of many different fluids over a wide range of flow rates, temperatures and pressures.
Due to their standardization, the expected measurement results are manufacturer independent.
Design features, constraints and error limits of the various differential pressure flow elements are described in detail in the ISO 5167 standard. Listed below is a general description of the different elements that we offer.
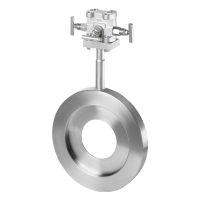
Orifice plates with integral taps are manufactured from a single body and therefore are cost effective. The pressure tapping takes place at two points. The instruments are easy to install and offer good accuracy with reasonable inlet and outlet runs.
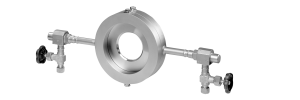
Annular chamber orifice plates consist of an orifice plate clamped between two annular chamber rings pressed together between standard pipe flanges. The pressure is measured upstream and downstream through the annular chambers. The accuracy is comparable to that of the standard orifice.

Meter Runs consist of the differential pressure element with inlet and outlet pipe sections. They are often used for small pipelines where pipe tolerances have a significant impact on the measurement accuracy. Typically, annular chamber orifice plate is used as the differential pressure element although other elements can be specified.
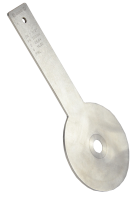
Paddle orifice plates for the installation between flanges or pipe taps consist of the orifice plate with a welded-on handle. The plates have no pressure taps and are therefore typically mounted between flanges containing ½” NPT pressure taps.
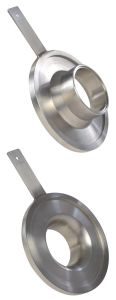
Nozzles are divided into two categories: ISA 1932 nozzles and long radius nozzles.
ISA-1932 nozzles are suitable for measuring flow rates of gas, steam and liquid. In the context of ISO 5167, they offer high accuracy with relatively low permanent pressure losses. Weld-in nozzles are often used in power plant applications with high pressures and temperatures. The tapping can be designed as corner taps, annular taps, flange ring taps, or socket ring taps.
Long radius nozzles are used in similar applications as the ISA-1932 nozzles and are available in the same design options as noted above. One of the advantages they have is excellent resistance to abrasion. One disadvantage is poorer linearity.
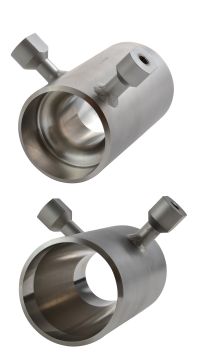
Standard Venturi nozzles are suitable for measuring flow rates in gases, steam and liquids. In the context of ISO 5167, they offer good accuracy with significantly lower permanent pressure losses compared to standard nozzles or orifice plates.
They have excellent wear resistance, but show reduced linearity compared to other differential pressure elements.
The tapping can be designed as corner taps, annular taps, flange ring taps, or socket ring taps.
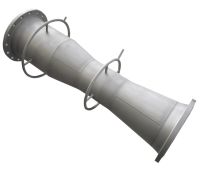
Classical venturi tubes are differential pressure elements with the advantages of very low permanent pressure losses and can be used in short straight pipe run applications. They have good measuring accuracy in their respective working ranges.
The taps can be designed as corner or annular chamber taps.

Cone flow meters consist of a pipe section with a cone welded inside. The cone size increases in the direction of flow. They are often used in applications with short available pipe runs.
With an error of +/- 5% of the measured value, it is the most inaccurate sensor in the ISO 5167 standard. When the cones are calibrated in a laboratory, they have a good accuracy.